Powder Coating Ovens Handling the Most Challenging Industrial Applications
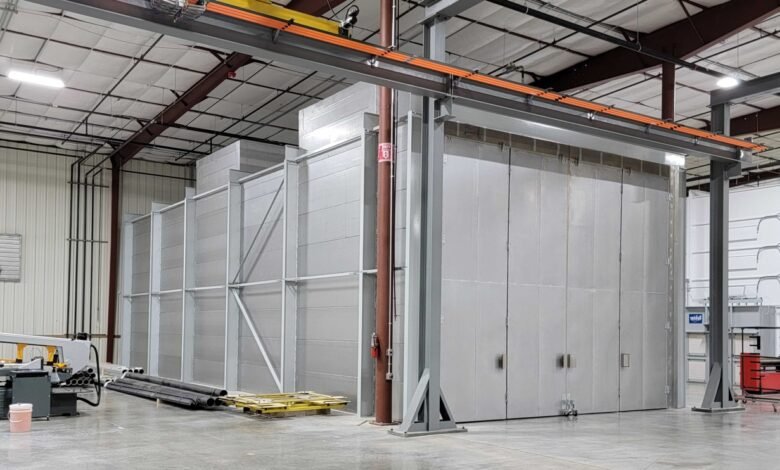
Powder coating ovens have become a linchpin in industries where top-quality finishes and durability are non-negotiable. From aerospace components to massive structural steel, these ovens are tasked with managing some of the most challenging applications. Each industry brings unique requirements, making powder coating ovens essential tools for consistent, high-quality results. Let’s explore how these remarkable machines rise to meet the challenges of various demanding sectors.
Read More: The Future of AI in E-commerce: Innovations and Trends
Tackling Heat-Intensive Curing for Heavy-Duty Machinery Components
Heavy-duty machinery components are built to withstand the harshest environments—think bulldozers, mining equipment, and other large industrial machines. To ensure these parts last, powder coating ovens must deliver uniform heat for efficient curing. High-temperature consistency is key, as these machines require robust coatings to resist rust, wear, and damage from heavy use.
Powder coating ovens handle heat-intensive curing by evenly distributing heat throughout their chambers, making sure every inch of these heavy components is uniformly treated. The high-capacity ovens used for such tasks are built to handle the size and weight of these components without sacrificing the consistency needed for a perfect finish. It’s all about providing a strong and even layer that holds up to the extreme conditions heavy machinery will face in the field.
Managing High-Precision Coatings for Aerospace Substrate Assemblies
When it comes to aerospace applications, precision is the name of the game. Powder coating ovens play a significant role in achieving the flawless surface finish required for aerospace substrate assemblies. These coatings are not just for looks—they must be smooth, lightweight, and durable enough to cope with extreme conditions like temperature fluctuations and high pressure.
For these high-precision coatings, powder coating ovens utilize sophisticated control systems to maintain exact temperature settings throughout the curing process. The ovens must create an environment where the powder cures evenly, preventing any imperfections or bubbles that might compromise performance. The precision of these ovens is what ensures that every component meets the rigorous safety standards of the aerospace industry.
Processing Large Structural Elements for Construction and Infrastructure
In the construction and infrastructure sectors, powder coating ovens are called upon to handle huge structural elements such as steel beams, bridge components, and support columns. These structures require protective coatings that can endure the elements, ranging from harsh UV rays to intense moisture and temperature changes.
Powder coating ovens used for these massive projects are designed to provide a high level of versatility. These ovens are often customized to accommodate long, heavy elements, offering ample space while ensuring heat is evenly applied from end to end. The result is a coating that delivers both aesthetic appeal and long-term durability, protecting essential structures against corrosion, rust, and weather-related damage.
Handling Multi-Layer Coating Requirements for Industrial Vehicle Frames
Industrial vehicles like trucks, forklifts, and agricultural machinery frames often require more than a simple layer of powder coating. Multi-layer coatings provide enhanced corrosion protection, ensuring these vehicles perform well under constant stress and exposure to tough environments. This is where powder coating ovens come into play, ensuring that each layer is cured perfectly before the next is applied.
Powder coating ovens designed for multi-layer applications maintain the precise temperature needed for each layer to cure fully. This is vital because any deviation might prevent the coatings from bonding properly, reducing the durability and longevity of the finished product. The ovens must ensure that each layer is cured without disturbing the ones beneath, resulting in a robust, multi-layer defense against the wear and tear these frames will endure.
Read More: The Important Role of Technology in Medical Accounting in 2024
Complex Geometries in Oil and Gas Sector Equipment
The oil and gas industry presents its own set of challenges for powder coating ovens, largely due to the complex shapes and geometries of the equipment used. From pipelines to valves and other irregular structures, achieving a uniform coating is no easy task. Powder coating ovens must tackle this challenge by providing consistent heat, even in those hard-to-reach corners and crevices.
To achieve this, powder coating ovens are often equipped with advanced airflow management systems. These systems ensure that hot air circulates efficiently, covering every part of the equipment without any cold spots. In the oil and gas sector, coatings need to resist both corrosion and chemical exposure, which makes uniform curing crucial to the equipment’s durability and safety.
Addressing High-Volume Production for Mass-Produced Metal Components
Mass production brings its own challenges. When thousands of metal parts need to be coated daily, powder coating ovens must keep up with the demand while maintaining the highest quality standards. These ovens are responsible for making sure that every part, whether it’s a car part, appliance component, or any other metal item, gets a consistent and durable finish.
Powder coating ovens used in high-volume production are often equipped with conveyors and automated systems that speed up the process while ensuring each component gets the necessary treatment. The ovens must be capable of handling continuous, high-throughput operations without compromising on the quality of the coating. Reliability and efficiency are key—these ovens must perform consistently to keep up with the demands of mass production.